从“精益”到“智慧” 广西汽车集团奏响“智造”进行曲
从“精益”到“智慧” 广西汽车集团奏响“智造”进行曲
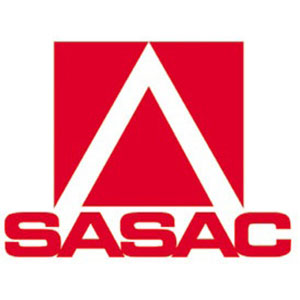
文章来源:广西汽车集团有限公司 发布时间:2018-12-28
一个两层楼高的立体仓库,随着堆垛机移动,物料完成自动扭转,一辆辆白色的AGV小车正从仓库自动取货,将配件驮送至不同的上料站台。物料在生产线上经过自动加工、装配、检测等繁复工序 ,被另外一批的AGV小车运转到出料口,等待送给客户。广西汽车集团井然有序、高效精准的自动化生产场面,今年在底盘智能工厂得以实现。
面对席卷全球的新工业革命,汹涌而来的产业互联网,广西汽车集团也深谋远虑,紧紧围绕“中国制造2025”这个当下炙手可热的国家级战略概念,深入讨论未来制造转型之路,努力实现由“制造”向“智造”转型。
借东风,开启蜕变之路
新一代信息技术与制造业深度融合,让汽车行业发生着一日千里的变革。广西汽车集团也在借助这股东风,挖掘制造新蓝海,促进产业再升级。
2007年,广西汽车集团引进第一台ABB点焊机器人,导入钣金件焊接自动化的新技术。2010年,在冲焊件产品开发中应用大批量机器人工作站,解决了钣金件外观及螺柱焊接质量问题,开始了大力提升公司的自动化装备水平之路。
2013年,广西汽车集团成立“自动化推进小组”,2015年升级为“工业4.0推进小组”,将智能制造纳入公司十三五规划中,围绕“一条智能生产线、一个智能车间、一个智能工厂”的思路,按照“工业2.0补课,工业3.0普及,工业4.0示范”的方式探索智能制造。一方面秉承公司一贯的精益制造理念和经验,打造精益生产融合智能制造的新模式,最大程度上提升生产效率和产品质量。另一方面结合工业物联网、云计算、大数据等新一代信息技术,探索数字化、智能化制造技术,使制造的重心向中高端产品和创新驱动转移,致力从传统生产转型智能化生产,争取站着智能制造这个风口实现弯道超车。
换档位,全面提速促转型
自动化焊接生产线整线开发是广西汽车集团自动化的成熟应用,已经超过一半以上产能利用机器人自动焊接实现。单单一条广西汽车集团河西冲焊件厂前地板生产线,流水线上的13台机器人一个小时自动焊接45个零部件,而同样的时间,27人工也是只能生产45个。
目前,广西汽车集团有工业机器人近1000台,其中冲焊件厂目前38条生产线中配置这157台机器人,自动化率达62%。机器人的应用领域在进一步扩展,从焊接,冲压,涂装、装配、检测以及物流过程都有机器人应用的亮点,生产效率及产品稳定性得到本质提高。
在已投入的10条数字化生产线中,大部分已经建成进入量产阶段,其中有两个工厂被柳州市工信委认定为数字化工厂。数字化生产线利用系统解决了生产过程的计划、排产、物流、工艺部署、质量控制、完工报工等业务衔接,实现了产品生产基本柔性化。
除了数字化生产探索之外,在物流、研发、营销、大数据等方面,也都展现了转型升级下的突破:
大力提升数字化供应链能力建设。硬件方面, 广西汽车集团建成了2个立体仓库,7个智能料架+AGV捡料配送单元,正在开展电子化单据及无人值守仓库的建设。其中,座椅整体智能仓储物流项目——海绵悬挂链,有效节约存储场地870m2,可优化2辆配送上线的拖车、4名拖车司机,减少约171个海绵料架的投放;座椅智能立体仓库与接驳系统,实现整椅下线出入库自动化,较传统模式减少用工8人/班。软件系统方面,建成了SCM+WOMS物流体系,完整实现了物流作业全过程管理,并实现了与客户计划的系统对接。
研发工艺输出数字化方面,正在与西门子合作建设五菱工业公司PLM系统,建成后,研发部门的工艺将可以与生产线进行对接,实现工艺部署数字化。另外,质量平台已完成一期建设,实现了质量的检验监控和质量问题管理。
立标杆,打造智能示范工厂
深耕智能制造,在广西汽车集团范围内开展智能制造装备的创新应用,工厂的自动化设备、智能化改造,智能化生产线和智能工厂建设逐步铺开,突破智能化生产过程中行业级的重点核心技术。
而这些投入,在缩短产品研制周期,提高生产效率和产品质量上的成效是惊人的。其中,在柳东乘用车零部件基地全自动焊接线模块,5条自动化焊接生产线及一条冲压生产线,81台机器人,自动化率达到76%,运行效率达到95%以上。今年新投入的山东分公司涂装生产线采用链式生产,上料、阴极电泳、涂装、检测、下料等环节均通过空中链条贯穿其中,可同时生产多种不同的产品,增加了输送产品的多样性和输送产品流向的任意性,实现生产的柔性化,节省人力18人,每件物料上线时间由6分钟缩短为1分钟,极大提高了生产效率。
智能工厂也在持续建设中,通过数字化、智能化的手段驱动“需求”、“研发”、“生产”、“服务”4端之间的互联协同,实现工厂全流程的数据采集和分析。作为汽车集团智能制造的深度应用试点,柳东乘用车底盘工厂以智能示范工厂为标杆,投入了一系列高科技与智能化系统,进行智能化在线检测与装备研发、柔性可视化装配装备研制,实现制造全过程透明化与智能化。该工厂属于公司“轻量化汽车底盘关键零部件智能工厂新模式”,并入围了国家工信部2017年智能制造综合标准化与新模式应用立项项目。
为了真正成为智能示范工厂,广西汽车集团可没少琢磨,因此在这个项目中诞生许多“第一次”,例如:厂房结构首次采用网架结构(24米柱距*24米跨距),充分保证了车间内的工艺布局和生产使用。全封闭空调温控厂房(25正负5度),维持了设备精度和稳定性;采用先进的噪音分析技术全功能分析和路谱模拟工况,全息NVH技术进行噪音诊断和能耗分析,部件总成减重11.65%,主减总成噪音控制在60分贝以下;全自动工艺过程参数和质量全过程精确追溯,准确率100%;建立公司基于VR/AR技术的产品3D数字化设计、虚拟仿真评估及其装配工艺规划平台;建立数据驱动的智能决策分析系统平台等等。
为进一步加快智能制造推进步伐,广西汽车集团还与国内外多家企业进行强强合作,在自动化改造方面,与上海诣谱进行资源整合,成为广西汽车集团的自动化改造推进力量;国际上,与ABB签订战略合作协议,以展开在机器人的深度应用以及柔性化生产的战略。与西门子合作建设PLM系统,以促成研发水平的提升以及输出可供数字化工厂直接利用的数字化工艺。与北京亚控合作建设数字化生产线标准,以迅速改造现有传统生产线。
千帆竞发,万木迎春。智能制造已是大势所趋,只有借助这股东风加速变革,不断加快技术创新,推进新旧动能转换,才在改变中看到希望和机会,打造企业的核心竞争力。广西汽车集团也将继续完善制造数字化建设,力争2020年实现制造和物流全面数字化,助力广西汽车行业转型升级,由大变强!
【责任编辑:李巨尧】