精益求精,向绿色航天迈出坚实一步
——长征四号乙运载火箭栅格舵落区控制系统诞生记
——长征四号乙运载火箭栅格舵落区控制系统诞生记
精益求精,向绿色航天迈出坚实一步
——长征四号乙运载火箭栅格舵落区控制系统诞生记
——长征四号乙运载火箭栅格舵落区控制系统诞生记
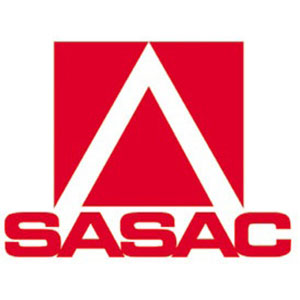
文章来源:中国航天科技集团有限公司 发布时间:2019-12-24
11月3日,在太原卫星发射中心,由航天科技八院研制的长征四号乙运载火箭带着4颗卫星升空。与此同时,在约600公里外的湖北省十堰市郧西县,栅格舵系统负责人陈雪巍抬头仰望、扫视天空。终于,在发射六七分钟后,一个小点出现在他的视野中,越来越大、越来越清晰,它就是完成任务的火箭一子级。这个长达27米、直径3.35米的大家伙最终落在了距离陈雪巍几公里外的石头山上。这一刻,他不是心惊胆战,而是心花怒放。
绿色航天 落区范围缩小85%
近年来,随着我国经济社会的发展,原来人烟稀少的内陆火箭落区逐步发展成人口稠密区域,再加上我国航天发射任务趋于高密度发展态势,落区环境安全成为大众关注的焦点。
在国外,火箭回收技术早已进入尝试阶段,有些国家已经取得过成功。在我国,精准控制落区一直是航天人研究的课题。随着技术的发展成熟,一子级栅格舵落区控制系统被提上日程。
长四乙火箭总设计师助理金益辉介绍:“之所以叫‘栅格舵’,是因为从外表看就像给火箭安装了4只小翅膀。这翅膀不同于普通的平面翼,它是镂空的,呈栅格状,让火箭看起来更像个大羽毛球。使用栅格舵系统,给无控的一子级装上‘翅膀’,让它不仅知道自己该往哪飞,而且还能飞到指定地点去。”
此次发射中采用的栅格舵是一种高效的新型气动稳定和控制舵面,具有很好的升力特性,紧贴箭体折叠安装,使用时再展开,不影响主任务飞行。栅格舵系统飞行试验的成功将大幅改善落区环境安全,为后续可重复使用运载火箭的研制奠定坚实的技术基础。
目前来看,该系统可以使一子级落区范围缩小85%以上,极大地改善和缓解落区环境的安全,避免大规模人员疏散、生命财产损失和有关纠纷,是积极履行社会责任和发展绿色航天的必然选择,在各方面都具有重要意义。
技术创新 高标准应对困难
全新的型号、全新的技术,可继承的太少、可借鉴的更少……自主创新是唯一的出路。
自开展研制工作以来,栅格舵系统设计团队、航天科技八院805所就高标准、严要求,通过自主创新、精益求精、刻苦钻研,研发出“耐热、轻质、坚固”可折展精准转动的栅格舵结构系统、低成本高集成度一体化电气系统和新模式独立测量系统。
栅格舵电气系统是控制栅格舵的“大脑”,它通过发送指令指挥舵面偏转,引导一子级箭体向目标点飞行。据陈雪巍介绍,设计团队摒弃传统繁杂的电气系统设计思路,选用了综合电子技术,将测量、导航控制、遥测等功能整合到一个长宽高都不到20厘米的小盒子中,大大简化了系统规模。
“此次创新使用了钛合金激光焊接成形的工艺方法。”栅格舵生产团队、800所宇航事业部栅格舵项目负责人周改超解释。
精益求精 初心匠心保障质量
栅格舵产品的结构看似简单,但尺寸精度要求极高,研制过程中须经过大量反复和试错,逐步摸索;产品从零件完工开始需经过组件装配、激光焊接、整体加工等多道工序,环环相扣,缺一不可。而这些必须由精益求精的匠心来保障。
在产品研制中,团队遇到的最大难题就是舵面的制造。“整个栅格舵由几十个部件互相卡箍和榫接组合而成,形成近50个网格节点,产生7种焊接厚度,焊缝数量多达500多条,需要采用6轴机器人配合直线导轨和两轴变位机,同时两面人工翻转和专用装置精确装配。”栅格舵系统生产团队、800所栅格舵项目技术负责人王业伟对于这些如数家珍。
为了解决这个难题,研发中心激光焊接负责人胡佩佩及焊接团队成员经过多次工艺方案专题讨论,最终确定了在产品零件精度符合设计图样要求的基础上,通过装配型架保证舵面装配精度,选用激光自熔焊工艺方法确保舵面整体质量的栅格舵研制工艺方案,有效解决了产品的工艺难题。
在不断地技术创新和精益求精中,栅格舵系统研制任务完美收官。然而,研制团队并没有满足于现有成绩。“不久的将来,我们将缩短栅格舵研制周期,降低研制成本,提高产品质量,实现栅格舵的批量化、半自动化生产。”周改超如是说。
【责任编辑:李子红】