兰州兰石集团:数智赋能助力兰石集团高质量发展
兰州兰石集团:数智赋能助力兰石集团高质量发展
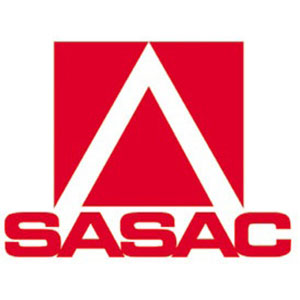
文章来源:甘肃省国资委 科创局 发布时间:2021-01-20
兰州兰石集团有限公司党委书记、董事长 阮英
随着大数据、云计算、人工智能等新兴技术的发展,以及信息化建设的不断推进,我国国有企业信息化工作,在经历了大规模建设、深化应用阶段之后,正在按照深度融合、创新应用的数字化转型方向发展。加快建设“数字企业”,推动企业向“数智企业”迈进,将数字化转型作为改造提升传统产业、培育发展新动能的重要手段,已成为国有企业的发展共识。党中央、国务院多次战略部署,大力推动国有企业数字化转型,增强竞争力、创新力、控制力、影响力、抗风险能力,提升产业基础能力和产业链现代化水平。
兰石集团作为大型能源装备制造企业集团,积极响应国家经济数字化转型、新型基础设施建设和甘肃省“三化”改造决策部署,以提升国家能源装备水平为己任,进一步强化数据驱动、集成创新、合作共赢等数字化理念,大力推进数字化、网络化、智能化发展,加快提质增效转型升级,着力打造成为具有数据洞察和产业整合能力的能源装备整体解决方案服务商。
夯实企业数字化转型基础
一是建设基础数字技术平台。近年来,兰石集团借助兰州市“出城入园”政策机遇,组织在新区产业园区建设主干网络、安防系统、数据中心等基础设施,构建以ERP、PDM、CAPP、MES为核心的销售、设计、采购到生产全生命周期管理系统,以及OA、门户、SOA、SRM、EAM、BI等业务支撑系统。同时运用云计算、大数据等新一代信息技术,自主研发了适应企业业务特点和发展需求的兰石云工业互联网平台,建设敏捷高效可复用的新一代数字技术基础设施,加快形成了集团级数字技术赋能平台,为能源装备行业数字化创新提供高效数据及一体化服务支撑。
二是建立系统化管理体系。先后组织编制《兰石集团信息化(两化融合)发展规划》《兰石集团智能制造发展规划》《兰石集团信息安全体系建设规划》,引领集团及各分子公司各级经营管理人员进一步提高加快推进数字化转型的理念和认识,为加快发展数字经济奠定良好基础。应用两化融合管理体系标准,加快建立数字化转型闭环管理机制,以两化融合管理体系促进企业形成并完善数字化转型战略架构。兰石集团成为甘肃省装备制造行业第一家通过两化融合管理体系现场评定的企业。
三是构建数据治理体系。围绕一切业务数据化、一切数据业务化的思想,构建数据治理与应用体系,加强生产现场、服务过程等数据动态采集,强化业务场景数据建模,深入挖掘数据价值,提升数据洞察能力。完成虚拟化安全管理系统、堡垒机等安全产品部署,加强平台、系统、数据等安全管理。使用安全可靠的设备设施、工具软件、信息系统和服务平台,提升数字化本质安全。为确保兰石数字化转型顺利实施,专门成立信息化和智能制造部门,组建以智能制造技术赋能产业转型发展的兰石爱特工业互联网公司,及专门规划引领、实施数字化工作的数据共享中心、技术开发中心等三级机构,系统推进兰石数字化转型工作。
加快推进产业数字化创新
一是推进产品创新数字化。利用物联网、大数据等技术来实现设备、人、系统之间的相互连接,推动换热机组、钻机、快锻压机等产品的数字化改造,更好地满足和引导用户需求。智慧换热机组,监测与控制换热机组进出口温度、压力、液位、流量、热量、频率、泵阀状态等运行参数,实现换热设备远程运维和无人值守,节省2/3的人力成本;智慧压机,采集压机设备锻压过程中的数据,建立锻压过程与产品质量关联关系,分析产品生产过程中“人机料法环”等过程数据,实现在线质量监测和异常情况分析,降低产品不良率;智能钻机,采集钻机运行过程中的数据,诊断设备或存在风险,预测设备及备件使用寿命,系统可延展为中石油、中石化、中海油等用户智慧油田提供对接支持。
二是推进生产过程智能化。兰石集团引进三维设计软件、分析仿真软件,加速产品设计从二维向三维转变,积极推进产品数字化创新,提升产品研发效率,产品研发周期缩短39.5%。利用物联网技术,实现产品智能化管理和控制,驱动工业设备向智能发展,提升制造企业产品竞争力。通过自主研发的MES系统,结合生产流程和产线、设备优化,打造智能工厂和数字化车间,打通订单、图纸、工艺、计划、工单、设备、工人、库存、质量数据流,重构生产模式,加快生产制造数字化智能化转型升级。兰石集团被评为工信部国家级智能制造试点示范企业。
三是推进管理运营智慧化。利用新一代信息技术,建立智慧环保、双重预防和能源管理等系统,实现生产运营的精细化和智能化管理。智慧环保系统,全面监控园区除尘设备和污水处理设备,加强环境监测和治理力度,大幅减少污水、粉尘对环境污染的影响,节能减排,促进经济可持续发展;双重预防机制,通过区块链和大数据技术分析安全风险及隐患,对安全风险进行分级管控,实时掌握安全风险分布和隐患排查情况,实现精准监管、巡察和指导,重大隐患整改率达100%,隐患总体整改率90%,有效减少了生产安全事故发生,集团2020年未发生重伤以上安全事故和环境污染事故;能源管理系统,通过对企业能耗数据进行采集、存储、处理、统计和分析,对企业能源消耗进行监控、分析和诊断,实现节能绩效科学有效管理及能源效率持续改进,实现了534个重点能源监测点数据采集、统计分析,全面强化能源管理精细度,2020年集团工业万元产值综合能耗同比上年下降10.51%。
四是推进用户服务敏捷化。基于物联网平台,实现了换热机组、快锻压机、智能钻机、环保设备、冶炼设备、供水供电等设备数据动态采集、在线监控、远程诊断、设备运行数据分析、设备故障报警、预测性维护等延伸服务,丰富完善服务产品和业务模式,同时助力设备运维单位产业升级,提升设备综合管理及运维水平。
打造行业数字化转型示范
一是构建智慧冶炼系统。结合大数据、云计算、人工智能等新技术,构建兰石铸锻冶炼产线智慧冶炼系统——铸锻大脑,通过对冶炼工艺进行优化,从原材料、冶炼到钢锭浇铸环节结合生产工艺、设备性能、安全运维、生产周期、产品性能等因素,通过数据建模、大数据分析、历史寻优等手段,实现部分产线、工序的“数字孪生”,为EAF炉、LF炉、VD炉推荐出最优生产运行及工艺配方参数组合,减少冶炼时长约10%,节省冶炼成本100万元/年。
二是打造焊接数字化车间。采用物联网技术,对重型压力容器焊接全过程进行数字化管控,实现145台焊接设备互联互通,现场焊接工艺参数数据采集覆盖率100%;实现焊接工艺编制、工艺管理、质量追溯与焊接质量准确评价;达到焊接工艺评定报告等评定规则使用正确率100%,焊接质量评价准确性高于90%,设计时间减少70%的目标。
三是打造兰石云工业互联网平台。基于新一代信息技术,贯穿设计、生产、管理、服务等制造活动各环节,自主开发兰石云工业互联网平台。平台采用“私有云+公有云”的混合云架构部署,构建了“三个企业应用门户”。内网门户建立统一身份管理平台,集成兰石已有信息系统,统一不同系统间用户身份信息;外网门户提供SAAS应用超市,为兰石产品客户和其他企业用户提供数据治理平台、物联网平台、企业管理云平台等工业应用,形成了云上业务解决方案;移动门户提供统一移动应用平台,整合员工沟通与数据流通工具,提高工作效率。
面向未来,兰石集团将积极融入数字经济发展时代潮流,聚焦支撑高端能源装备制造主责主业转型升级发展目标,充分利用工业互联网、大数据、云计算、5G+、区块链、人工智能等信息技术,紧紧依托在离散型制造业信息化整体规划、软件开发、业务实施及IT基础设施运维等方面经验,加大5G网络基础设施投入,扩充壮大企业数字化专业人才队伍,大力探索离散型制造行业智能制造新型模式,加快推进数字产业化、产业数字化能力提升和对外复制、赋能能力,力争用3—5年时间建设以5G+数字化车间/智能工厂为方向的离散型智能制造标杆,着力打造甘肃省乃至西北地区具有较大影响力的离散型工业互联网平台集成和系统解决方案服务商,助力甘肃工业企业转型升级和全省经济高质量发展。
【责任编辑:赵艺涵】