中国石化天津百万吨乙烯及配套项目建成投产
中国石化天津百万吨乙烯及配套项目建成投产
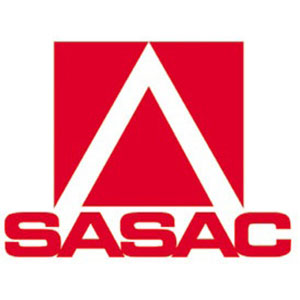
文章来源:中国石油化工集团公司 发布时间:2010-01-19
1月16日,国内规模最大的百万吨乙烯单套装置之一——天津石化100万吨/年乙烯装置一次开车成功,生产出合格产品,标志着中国石化天津百万吨乙烯及配套项目全面建成投产。
中国石化天津百万吨乙烯及配套项目具有世界级规模和一流工艺流程、生产技术,是目前在建同类装置中国产化率最高的。该项目可拉动天津工业总产值4%以上,带动下游上千亿元投资,是滨海新区经济发展的重要引擎。
天津乙烯工程工艺流程全部打通,创造了中国北方严寒条件下一次开车成功的新纪录。
该项目是国家和中国石化“十一五”重点建设工程,是天津滨海新区开发开放标志性工程和天津建设国家级石化产业基地的龙头项目。项目主要包括100万吨乙烯、1000万吨炼油、热电工程和区外工程四大部分,共205个工程主项。工程总占地面积297公顷,项目主体建设投资268亿元,加上配套工程,达到340亿元。2004年3月16日,国务院正式批准天津大型乙烯工程立项。2005年12月22日,国家发改委正式核准天津乙烯项目。2006年6月26日,项目开工奠基。2009年12月21日,配套项目1000万吨炼油工程打通全流程并生产出合格产品,实现一次开车成功。
该项目具有集约性、先进性、创新性、环保性和经济性特点。新建炼油装置全部设置在老厂区内,通过优化整体布局,合理配置装置结构,实现联合布置、集中控制、统一管理,现有资源得到充分利用。整个项目,特别是乙烯工程8套装置均达到世界级规模。其中,100万吨乙烯裂解为国内规模最大的单套装置之一,45万吨聚丙烯为全球规模最大的单套装置。通过技术引进和技术创新,主要生产装置拥有世界上最先进的工艺流程和生产技术。项目的生产管理模式与国际先进石化企业接轨,工艺操作采用集中控制,人员精干高效,达到国际先进水平。乙烯工程与国外公司进行合资合作,引进先进的管理经验和工艺技术,实现“强强联合、优势互补”,进一步提升了企业的核心竞争力。
该项目是目前在建同类装置中国产化率最高的项目,炼油和乙烯设备国产化率分别达到91.5%和78%,有力地提高了国内装备制造业水平。除部分装置引进国外专利使用权和技术工艺包外,炼油基本上采用国内技术,乙烯大部分采用国内或合作开发技术,自主创新能力得到进一步提高。
中国石化高度重视环境友好和可持续发展,项目环保总投入超过20亿元,不但使新建装置实现达标排放,而且通过实施“以新带老”项目,使二氧化硫、烟尘和固体可吸入颗粒物的排放量在现有程度上均有不同幅度的下降,天津石化整体环保水平得到提升。同时,通过采用新工艺和新技术,汽柴油质量达到欧3以上排放标准,可为社会提供高质量的清洁能源。整个项目依托现有装置建设,新征土地均为盐碱荒地,所增加的每天约9万吨工业用水全部通过海水淡化解决,水资源的重复利用率达到97%以上。由于采用新工艺和新技术,乙烯综合能耗为580千克标油/吨,炼油综合能耗为69.51千克标油/吨,达到国际先进水平。
该项目建成投产使天津石化炼油一次加工能力达到1500万吨/年,乙烯生产能力120万吨/年,成为全国最大的乙烯生产企业之一和华北地区最大的炼油加工基地,每年可为社会提供高质量成品油587万吨、乙烯等化工基础原料320万吨、高端合成树脂和化纤150万吨、液化气等其他产品75万吨,对满足国民经济增长的需要,加快我国石化工业发展、积极应对国际石化产业发展新趋势具有重要的促进作用。
该项目不仅带动了天津市氯碱工业的结构调整和优化升级,而且也将推动滨海新区乃至天津经济的发展。初步测算,该项目可拉动天津工业总产值4%以上,并带动下游产业及配套工程投资约1000亿元。