科技赋能 河钢集团全力打造智能绿色工厂
科技赋能 河钢集团全力打造智能绿色工厂
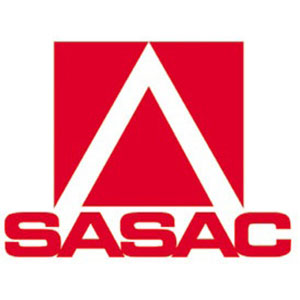
文章来源:河北省国资委 发布时间:2022-09-15
进热轧脱硫站平均铁水温度比课题开展初期提高25℃;铁水包周转率从2.4次/天提高到3.0次/天以上;板坯热装平均温度比课题开展初期提高79℃;以7月份产量和品种结构测算,单月降本约1898万元。日前,河钢集团关于“唐钢新区流程优化和智能化运行项目”(以下简称“项目”)阶段汇报会在北京举行,一组组成果数据令在场人员喜悦和振奋。
项目正式启动一年来,河钢集团经过各方协同推进、共同努力,打造世界级新一代全流程智能工厂典范的目标更明、信心更满,依靠科技创新和技术进步实现技术领先的道路,走得更加坚定。
强强联手 致力打造行业标杆
随着时代发展,中国钢铁工业面对资源能源供给、实现低碳绿色、保护环境生态、融合信息化、智能化技术等诸多挑战。相关专家深入思考钢铁工业的发展趋势,提出了一个新的冶金学科学术领域——冶金流程工程学。新的理论体系将冶金学的知识上升和拓展到流程层次,站在工程科学的立场上打通制造流程。
唐钢新区作为践行新发展理念、推动河钢集团转型升级高质量发展的重点示范项目,拥有一流的流程、装备、信息化和人才基础。去年4月,河钢集团与中国钢研科技集团签署《唐钢新区流程优化与智能化运行项目合作协议》,积极推动中国钢铁工业智能化发展。9月,项目正式启动,各项工作有序展开——
统一思想,凝聚合力。多次召开交流会、协调会,项目各方深刻理解项目实施重要意义,河钢集团站在引领全行业智能化发展的高度做顶层设计和战略规划,唐钢把项目提升到整个公司战略层面上进行安排部署。
深入调研,充分交流。相关专家带领项目团队,深入开展课题准备和设计工作,6个月内开展了2套问卷调查、5次现场调研和1次运行实绩数据分析。
明确方向,细化任务。明确方向目标、关键问题、技术路线和研究内容,在总体设计协同、工艺优化、界面优化和动态调度、质量优化、数据分析平台等5个层面设置7个课题。
加强管理,完善架构。集中优势资源,设5个专业组,支撑项目运行,解决关键问题;设7个项目经理部,具体实施项目课题。
各司其职,高效协同。中国钢研专家团队和唐钢各部门专业技术人员共同开始了现场业务调研和技术攻关。唐钢每周组织课题调度会,并制定双周滚动计划;河钢集团每月组织项目推进会,协调解决问题,管控课题进度和质量。
创新引领,锻造产线“顶端对话”硬实力
初秋的唐钢新区碧空如洗,蓝天下一列拉着铁水包的火车从唐钢炼铁3号高炉炉下缓缓驶出。技术攻关团队密切跟踪着铁水运输过程每个作业环节:火车准时到,铁水进入热轧脱硫站的温度达到1395℃。项目攻关以来,该指标平均值较攻关初期提高25℃,经测算,实现吨钢成本降低7.44元。
“唯有科技创新和技术进步,才是企业发展的灵魂。”唐钢深刻理解河钢集团技术升级新发展阶段的战略目标,明确发力点:“依托项目,学习国际一流的工艺技术和先进理念,积极推进工艺创新和管理创新,破解产线难题,锻造与一流企业同台竞争的硬实力。”
该项目凝聚了多年的理论研究成果和工程实践经验,抓住了制约唐钢新区流程优化与智能化运行水平提升的关键问题,其“靶心”在产线。瞄准“靶心”,精准发力。各课题组按需求分析、概要设计、详细设计、开发测试、功能上线的项目流程制定了详细的工作计划。
界面优化、动态调度是智能化运行关键环节。炼铁—炼钢界面优化和动态调度课题组为了给铁水“保温”下足了功夫。从高炉出铁控制技术研究到铁水温度波动因素分析,从建立温度预测模型到界面物质流匹配模式优化,唐钢生产制造部副部长马新光与课题组成员一道,进行了大量的数据分析,并一遍遍推演、模拟、试验。
面对全新的“一包到底”生产组织模式、全新的铁运线路,唐钢生产制造部调度指挥中心针对8个运行场景与2个应急场景,进行了为期一个月的铁包周转全流程模拟。
克服多个难题,课题组最终确立了炼铁—炼钢界面包括出铁、炉下配包、接铁、空重包组列等在内的综合运行工艺规则库,实现了指标跃进、成本降低。
板材炼钢区段“一对一”层流协同运行课题,涉及铁水脱硫、转炉炼钢、钢水精炼、连铸等多个工序环节,全流程、系统性和跨部门协同在课题推进中亦十分重要。为突破难点,团队改进作业步骤,改造氧枪喷头,优化工艺,自主开发转炉一键式自动出钢,实现转炉周期稳定控制在30分钟以内,而国内先进钢企200吨以上大型转炉冶炼周期约为40分钟。目前,该课题组初步建立了两条刚性层流运行专线,典型钢种“一对一”层流专线率从攻关初期的38%提高到了66.3%。
除铁钢界面区域、钢区界面区域,铸轧界面通过板坯排队优化,热装率也得到显著改善,提高了15%。
经过一年多的攻关,项目课题中期各项任务均已完成,需求分析及概要设计阶段任务全部完成。各课题组以物质、能量、时间、空间、信息“五维”为核心,从全流程视角进行工序优化和跨工序协同,各个工序、界面和流程的能量损失和物质消耗得到明显优化。经测算,全工序吨钢成本降低31.94元。
生根开花,汇聚建立新比较优势的核心力量
项目的实施为唐钢科技创新和技术进步工作注入了全新的理念,带来了新的思维方式,以及新模式、新路径。
一年来,除收获了降本增效的“真金白银”,更多更深层次的改变也在悄然发生——
思路更宽,眼界更广。落实“把工程做到极致”的工程哲学理念,各单元对主工艺以外的细节,研究得更加广泛、深入和细致。职工主动统计各工序最小单元动作时间,并优化各最小作业单元顺序。钢区动态调度课题开展后,天车作业区规范天车运行的各动作点位,提高作业效率;通过改进水口更换方法、细化和分解钢包热修微观流程作业、推进钢包滑板多连滑等措施,大大缩短钢包准备时间。炼钢调度室完善天车作业规程12项,缩短空包待吊时间。
密切协同,刚性连接。在冶金流程工程学的理论指导下,各工序摒弃“各自为战”的思想,跨工序、跨部门或多工序、多部门协同工作,从工序生产、组织调度、运维服务等整体协同更加密切、高效。通过开展铁钢区界面优化攻关,炼铁与炼钢之间的工序衔接更加紧密,铁水包周转率达到3.0次/天以上。
固化标准,管理精准。运用科学理论工具,将已经确定的优化工作纳入到标准、作业文件中,实现工艺、生产模型与智能化软件的充分融合,努力达到“管理靠制度规范、制度靠流程落地、流程靠系统固化”。
开放环境,培养人才。项目实施过程中,企业为科技创新和技术进步创造了全新的开放式环境,营造了崇尚技术进步、尊重科技人才的浓厚氛围,技术人员深度参与到智能制造的创建过程中。通过在课题中的摔打和磨练,企业培养了一批既懂工艺流程又懂信息化工作的复合型人才。
智能化发展是新时代钢铁工业高质量发展的强大杠杆之一,是技术进步的核心。智能化的定义是要构建一个数字物理融合系统,是一个系统性、全局性、开放动态性的命题。智能化系统必须是整体系统性、动态协同性、自感知、自学习、自决策、自执行、自适应的大系统的智能化。
“项目的不断推进和取得的累累硕果更加坚定了我们实现最终目标的信心!”唐钢集团的员工信心满满,将依靠科技创新和技术进步实现技术领先,努力创建数字化智能化的未来工厂。
【责任编辑:语谦】