首钢以创新推动煤气资源高效利用纪实
首钢以创新推动煤气资源高效利用纪实
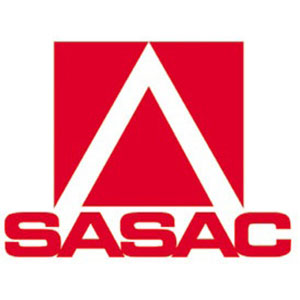
文章来源:中国钢铁新闻网 发布时间:2007-06-21
首钢以创新推动煤气资源高效利用纪实
煤气资源的高效利用是冶金行业节能减排,大力发展循环经济,全面推行清洁生产,形成低投入、低消耗、低排放和高效率的有效节约方式。近年来,首钢以创新为手段,狠抓二次能源的回收利用,使煤气回收率大幅提高,以转炉煤气为例,2004年吨钢煤气回收率仅为63.3立方米,而今年前5个月,首钢转炉煤气吨钢回收率达到99.85立方米,列全国同行业首位。
近年来,首钢加大科技创新力度,实施一系列技术攻关和改造,不断创新生产组织新形式,科学平衡煤气调度,使首钢煤气资源的回收利用效果突出。特别是2006年5月以来,焦化厂二焦炉停产后,使焦炉煤气、转炉煤气等高热值煤气的供应更加紧张。为解决这一问题,利用第二和第三炼钢厂实施负能炼钢的时机,首钢改造了动力厂煤气混合站煤气管网,将高峰时富裕的转炉煤气串入高炉煤气管道中,提高了转炉煤气回收量。首钢还对精品棒材煤气系统进行改造,将原来只有高炉和焦炉煤气混合使用的方式,改造成为高、转、焦三种都能混合使用,不仅减少了焦炉煤气的使用量,同时提高了热值,为精品棒材顺利达产创造了极为有利的条件。
为减少高炉煤气放散,使首钢的煤气资源得到充分利用,今年4月,首钢总公司生产部、设备部、设计院、动力厂等部门和单位经过缜密研究,科学探讨,在安全范围内,提高高炉煤气放散压力,由原来的10KPa,提高到12KPa,运行2个月来,炼铁厂高炉热风炉使用煤气压力相应提高,燃烧效果明显见好。同时,炼铁厂五制粉煤气系统改造项目实施后,彻底实现了用高炉煤气替代焦炉煤气的转变,每年可为总公司节约焦炉煤气2000万立方米,多用高炉煤气8000万立方米,既为轧材生产提供了高热值的煤气,又为减少高炉煤气放散起到积极的作用。今年,首钢还对电力厂4号炉进行技术改造,使4号炉高炉煤气使用量比去年每小时多用1500立方米。经过努力,首钢高炉煤气放散率由2005年的16.4%,降至今年前5个月的10.2%。
首钢过去没有焦炉煤气储存柜,生产高峰时焦炉煤气紧张,轧材厂周修或检修时煤气又相对过剩。针对这一问题,首钢今年初投资180余万元,将动力厂煤气加压二站2号转炉煤气储存柜改造为焦炉煤气储存柜,在焦炉煤气管网压力高时利用气柜储气,夜间生产节奏快煤气压力低时向管网释放。生产部组织有关部门以最快的速度完成了设计方案讨论、施工组织、运行方式调整、相关设备检修等工作, 6月4日正式投入运行。运行仅10天,累计平衡焦炉煤气近50万立方米,产生了可观的经济效益。
创新生产组织管理新形式,为煤气资源的利用提供有力保证。今年以来,首钢生产部以能源的最充分利用为目的,加强部内沟通,合理组织生产。首先,把过去检修时定修一周安排三天,改为一天安排一个车间检修,为合理使用煤气创造条件;其次,在炼钢生产中,严格控制炼钢节奏,保证转炉煤气均衡产生,均衡用气;在安排精棒、线材、型材、中板生产计划时,注重品种规格搭配,避免了因大规格品种集中生产造成煤气供应紧张和小规格品种集中生产带来煤气相对过剩的问题。自去年11月份至今年3月份,在二焦炉停产减少煤气量,轧材产量提高14万余吨的情况下,冬季生产烧油5000吨,较上一年度直接节约6500余吨,创经济效益1400余万元。